Raw material control is a critical measure to ensure product quality, minimize environmental impact, and maintain compliance with technical requirements for environmentally labeled products. Let's delve into the significance of raw material quality control and effective management strategies.
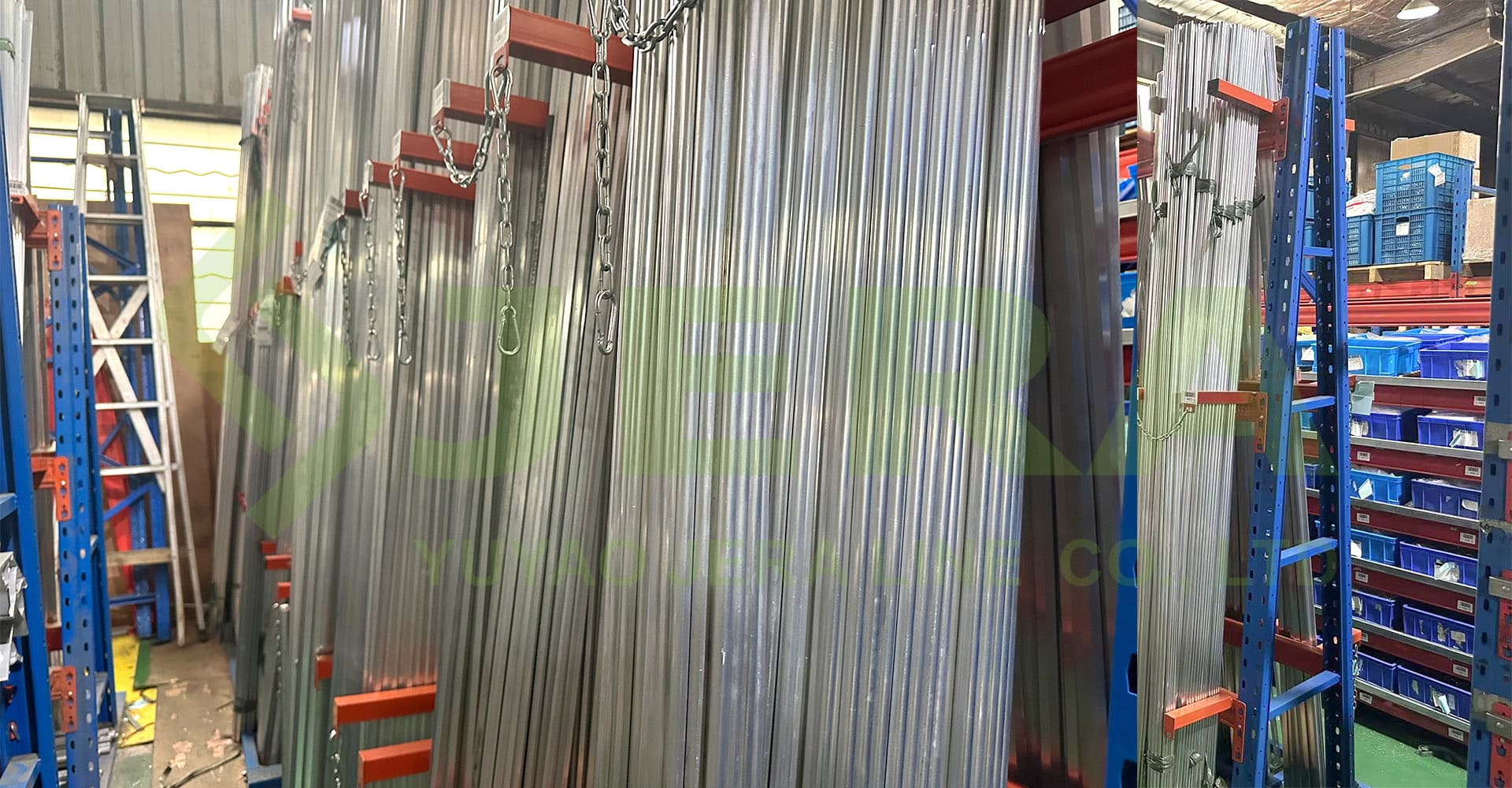
Importance of Raw Material Quality Control
-
Ensuring Final Product Quality: The quality of raw materials directly impacts the performance, reliability, and durability of the end product. Flawed raw materials can adversely affect the final product.
-
Avoiding Production Disruptions: Low-quality raw materials can lead to production interruptions, increased costs, and delayed deliveries. Strict control over raw material quality mitigates these risks.
-
Reducing Defect Rates: High-quality raw materials contribute to lower defect rates. This not only enhances customer satisfaction but also reduces post-sales maintenance costs.
Steps for Raw Material Quality Control
-
Incoming Material Inspection: Rigorously test and control the chemical composition, physical properties, and other aspects of raw materials during procurement to ensure compliance with standards.
-
Process Quality Control: Monitor each production process step to prevent contamination or other quality issues affecting the product.
-
Finished Product Quality Control: Conduct comprehensive inspections on the final product to ensure adherence to quality standards.
-
Continuous Quality Improvement: Continuously improve the raw material quality control process to adapt to market demands and technological changes.
At JERA LINE, we implement rational production scheduling to ensure normal machine operation. We have also developed operational manuals to facilitate continuous learning and improvement among our staff. Additionally, dedicated personnel oversee production quality during the manufacturing process, minimizing defects and thereby reducing raw material losses.