Introduction
Choosing the right mechanical cable connector might seem like a small detail, but it's one that can have a significant impact on the efficiency and reliability of your system. Whether you're working on a complex industrial setup, a piece of heavy machinery, or a more straightforward project, the right connector ensures that your cables are secure, well-organized, and capable of withstanding the environmental and operational stresses they'll encounter.
In this article, we'll dive deep into everything you need to know about mechanical cable connectors. We'll explore what they are, why they matter, and most importantly, how to choose the right one for your specific needs. By the end of this guide, you'll be well-equipped to make an informed decision that will keep your cables—and your projects—running smoothly. Let's get started!
What are Cable Connectors?
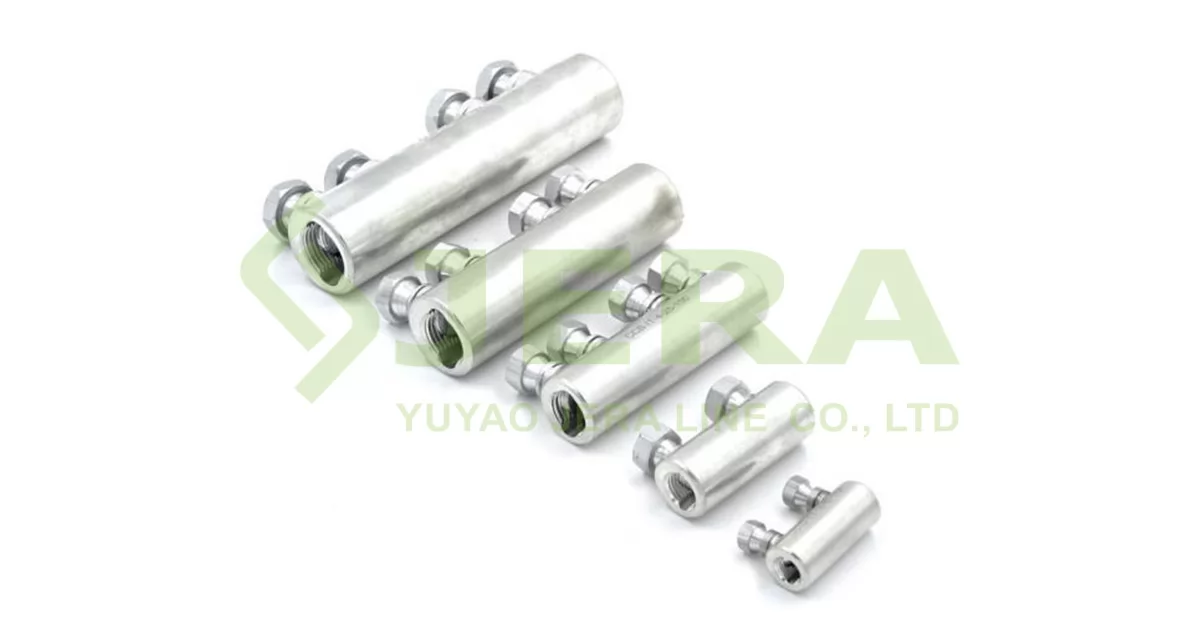
Cable connectors are essential components used to join electrical or mechanical cables to various devices, systems, or other cables. They serve as the critical link that ensures a secure and reliable connection, facilitating the transmission of electrical signals or mechanical force from one point to another. Whether in industrial machinery, automotive applications, or simple home electronics, cable connectors are ubiquitous and indispensable.
There are various types of cable connectors, each designed for specific applications and environments. These connectors can range from simple plug-and-play designs to more complex assemblies that require precise engineering to meet stringent performance requirements. In mechanical applications, cable connectors are designed not only to hold cables securely but also to protect them from environmental factors such as moisture, dust, and vibrations. They are typically constructed from durable materials like metal or high-grade plastics, ensuring longevity and resilience under demanding conditions. Understanding the different types of cable connectors and their specific uses is crucial for anyone involved in mechanical engineering, electrical work, or any field where cable management plays a key role. Let's delve into the details of these connectors and their functionalities in the following sections.
How to Choose the Best Mechanical Cable Connector for Your Application
Understand Your Application Requirements
The first step in choosing the right mechanical cable connector is to thoroughly understand the requirements of your application. Consider the following:
-
Load and Tension: Determine the amount of load or tension the cable connector will need to withstand. For heavy-duty applications, such as in construction or industrial machinery, you’ll need a connector designed to handle significant mechanical stress.
-
Environment: Consider the environment where the connector will be used. Will it be exposed to extreme temperatures, moisture, chemicals, or vibrations? Connectors designed for harsh environments typically feature robust materials like stainless steel or corrosion-resistant coatings.
-
Movement and Flexibility: Assess whether the cables will need to move or flex during operation. For applications that involve frequent motion, such as in robotics or automated systems, you’ll want connectors that can accommodate flexibility without compromising the integrity of the connection.
Choose the Right Material
The material of the connector plays a critical role in its performance and longevity. Mechanical cable connectors are typically made from materials such as:
Material Type Selection Table
Material |
Characteristics |
Common Applications |
Stainless Steel |
High strength, corrosion-resistant |
Marine, industrial, outdoor environments |
Aluminum |
Lightweight, durable |
Aerospace, automotive |
Plastic/Polymer |
Electrical insulation, chemical resistance |
Automotive, consumer electronics |
Brass |
Good conductivity, corrosion-resistant |
Electrical systems, instrumentation |
Connector Type Selection Table
Connector Type |
Advantages |
Ideal Use Cases |
Crimp Connectors |
Strong, reliable connections without soldering |
Electrical, automotive |
Clamp Connectors |
Secure grip, ideal for vibrations |
Heavy-duty, industrial machinery |
Threaded Connectors |
Secure, waterproof |
Harsh environments, outdoor applications |
Quick-Connect/Disconnect Connectors |
Convenient for frequent use |
Testing, maintenance, modular systems |
Evaluate the Connector Size and Compatibility
-
Cable Diameter: Ensure compatibility with the cable’s diameter and insulation.
-
Connector Standards: Verify if the connector meets industry standards or certifications.
Ensure Safety and Compliance
-
ISO Standards: Verify adherence to international quality, safety, and efficiency standards.
-
UL Listings: Check for safety certifications from Underwriters Laboratories.
-
RoHS Compliance: Ensure the connector is free from hazardous substances.
Test and Validate the Connector
-
Prototyping: Assess performance with a small batch in real-world conditions.
-
Stress Testing: Subject the connector to extreme conditions to verify its capability.
-
Long-Term Reliability: Consider the expected lifespan and maintenance of performance over time.
Conclusion
When in doubt, it’s always a good idea to consult with experts or directly with connector manufacturers. They can provide insights into the best options for your specific application, including custom solutions if standard connectors don’t meet your needs. Choosing the right mechanical cable connector requires careful consideration of various factors, from the application’s demands to material and safety standards. By following these steps, you can ensure that your connector choice will deliver the reliability and performance necessary for your system's success.